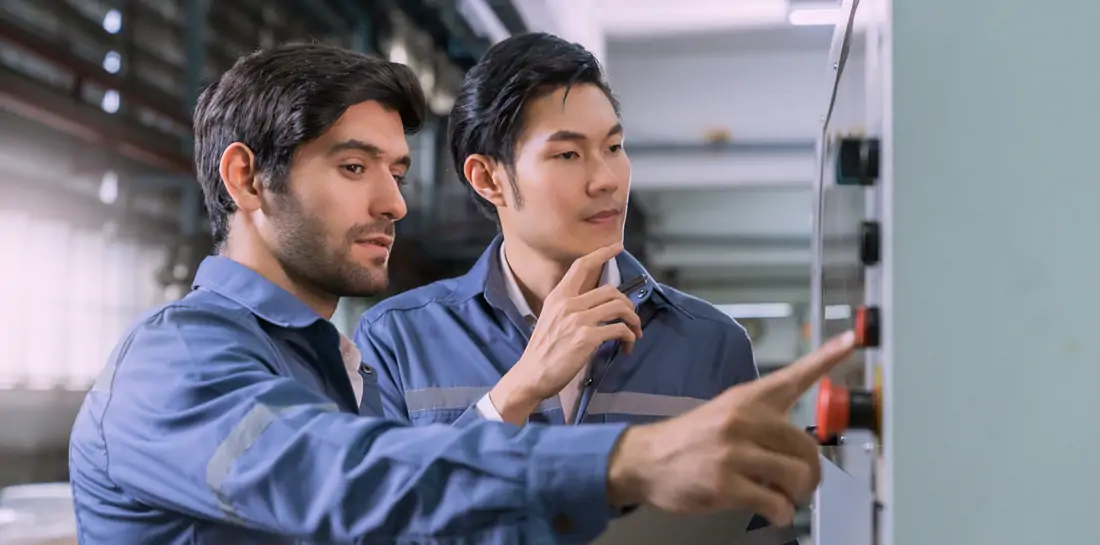
TPM & Ergonomics
Efficient production requires well-maintained machinery and an ergonomic work environment.
Our Total Production Maintenance & Ergonomics (TPM & E) service helps clients evaluate maintenance strategies, identify ergonomic risks, and implement sustainable improvements to optimize both machine efficiency and worker safety.
We integrate Total Productive Maintenance (TPM) principles with ergonomic assessments to reduce downtime, improve workforce well-being, and enhance overall equipment effectiveness (OEE).
Activity Indicators
Maintenance Cost Distribution (%)
Major Initiatives
Optimizing machine reliability & worker safety:
- Assess current maintenance strategies to identify inefficiencies and risks.
- Apply TPM methodologies to enhance predictive and preventive maintenance.
- Conduct ergonomic risk evaluations to ensure safe and sustainable work conditions.
- Optimize machine workload to reduce Muri (overburden) and enhance efficiency.
- Develop training programs for employees on safe and effective equipment handling.
- Implement smart monitoring solutions to track equipment performance in real-time.
Frequently Asked Questions
TPM focuses on reducing unplanned downtime, increasing machine availability, and improving equipment lifespan, leading to enhanced productivity.
Ergonomic improvements reduce workplace injuries, enhance employee well-being, and contribute to long-term operational efficiency.
A TPM & Muri analysis report including machine maintenance strategy evaluations, ergonomic risk assessments, and detailed improvement recommendations.
Customer Benefits
Well maintained production and safe work environment lead to higher productivity, reduced operational costs, and improved employee well-being. By integrating TPM strategy with ergonomic assessment, companies can reduce downtime, improve workplace, and optimize OEE.
- Minimized machine downtime – through predictive maintenance strategies.
- Reduced ergonomic risks – leading to higher workforce efficiency and satisfaction.
- Lower operational costs – by optimizing resource utilization.
- Improved equipment lifespan – with structured TPM methodologies.
- Enhanced workplace safety – Company, Industry, Market Research
- Plombett – with proper Muri (workload) reduction plans.
- Higher overall equipment effectiveness (OEE) – with streamlined maintenance.