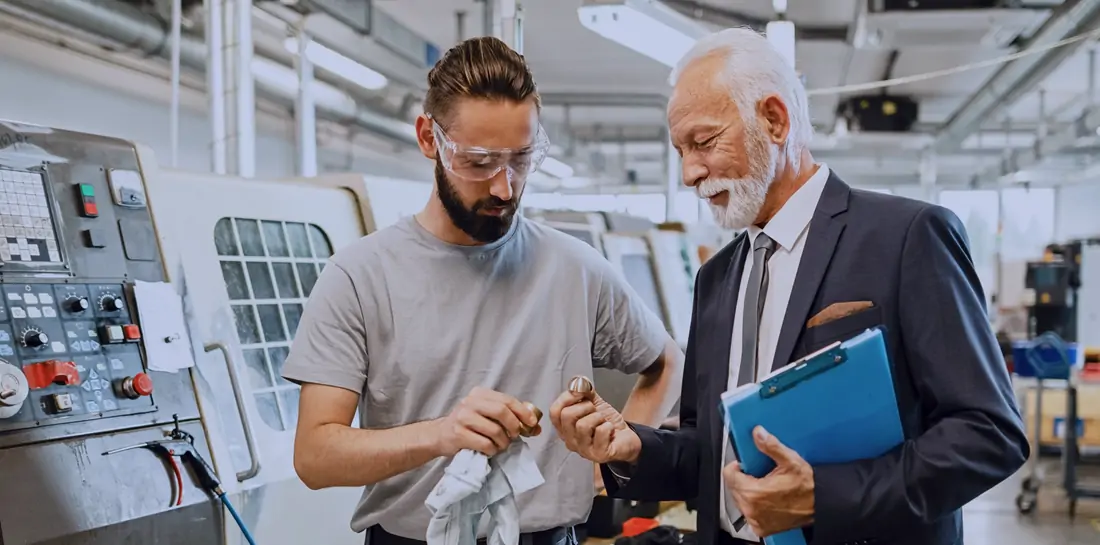
Process Quality Validation
Process quality validation is a critical component of manufacturing excellence, ensuring that production processes meet stringent quality standards, reduce variation, and enhance defect prevention.
Our Process Quality Validation service includes VDA 6.3 process audits, comprehensive defect analysis, and real-time process control solutions to ensure consistent and high-quality output.
From Variability to Precision: Validate & Standardize Your Production Processes.
Activity Indicators
Process Quality Compliance Scores – VDA 6.3 Audit Scores, Defect Rates, Process Stability
Major Initiatives
Ensuring end-to-end process validation through audits, inspections, and control systems.
- VDA 6.3 Process Audits – Conduct structured evaluations to assess process maturity and risk areas.
- Advanced Defect Analysis – Apply Root Cause Analysis (RCA), 8D methodology, and FMEA for proactive issue resolution.
- Statistical Process Control (SPC) – Implement real-time quality monitoring and predictive analytics.
- Gage Repeatability & Reproducibility (GR&R) Studies – Ensure measurement accuracy through MSA (Measurement System Analysis).
- Production Process Optimization – Eliminate bottlenecks and standardize manufacturing processes to improve efficiency.
- Supplier Process Quality Management – Align suppliers with best-in-class quality expectations through VDA 6.3-based assessments.
Frequently Asked Questions
VDA 6.3 is a structured process audit framework developed by the German automotive industry, ensuring risk-based quality management in manufacturing.
SPC (Statistical Process Control) monitors production performance in real time, identifying process variations before defects occur.
Best practices recommend quarterly VDA 6.3 audits and continuous monitoring of process stability indicators (CpK, PpK, etc.).
Customer Benefits
Standardizing and validating processes leads to higher efficiency, cost reduction, and better customer satisfaction.
- Stronger Process Stability – Improve CpK & PpK values for consistent production.
- Lower Defect Rates – Proactively reduce quality issues through structured validation.
- Regulatory Compliance – Meet IATF 16949, ISO 9001, and VDA 6.3 requirements.
- Higher Supplier Performance – Align suppliers with industry best practices.
- Reduced Production Costs – Minimize rework and scrap through process control.
- Enhanced Customer Confidence – Deliver reliable, defect-free products with proven quality control.