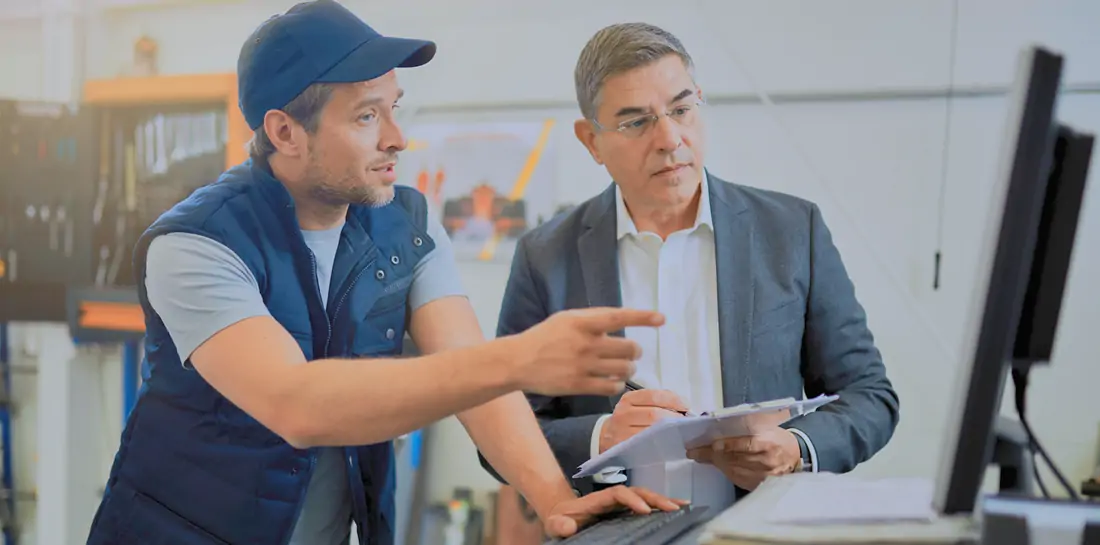
On-site Audit & Assurance
Ensuring supplier compliance and process quality is essential for risk mitigation, regulatory adherence, and continuous improvement.
Our On-Site Audit & Assurance service provides in-depth assessments, covering APQP, PPAP, MSA, and SPC, to enhance product quality, manufacturing consistency, and supplier reliability.
From Compliance to Excellence: Strengthen Supplier & Process Quality Through Audits.
Activity Indicators
Supplier Audit Compliance Rates – Audit Performance by Category
Major Initiatives
Our structured audit framework ensures full compliance and continuous supplier improvement.
- Advanced Product Quality Planning (APQP) — Ensure structured quality planning across product development.
- Production Part Approval Process (PPAP) — Verify supplier capability to meet engineering requirements.
- Measurement System Analysis (MSA) — Ensure accuracy and reliability of measurement systems.
- Statistical Process Control (SPC) — Implement real-time monitoring for process stability.
- Supplier Corrective Action Management — Identify root causes and drive long-term improvements.
- Regulatory & Industry Compliance Audits — Align with global standards such as ISO 9001, IATF 16949, and VDA 6.3.
Frequently Asked Questions
Regular audits (quarterly or annually) ensure sustained supplier performance and quality assurance.
PPAP ensures that suppliers consistently produce parts that meet design specifications and maintain quality over time.
Yes, SPC implementation can be adapted to existing processes, providing real-time quality monitoring and defect prevention.
Customer Benefits
Comprehensive audits drive continuous improvement, supplier accountability, and long-term quality assurance.
- Minimized Quality Defects – Ensure compliance through APQP & PPAP validation.
- Improved Measurement Accuracy – MSA guarantees repeatable and reproducible data.
- Enhanced Process Stability – SPC implementation reduces variation and defects.
- Stronger Supplier Relationships – Proactive quality assurance fosters collaboration.
- Regulatory Risk Reduction – Meet global compliance standards and industry benchmarks.
- Higher Customer Satisfaction – Deliver reliable, high-quality products with consistent performance.