TPM & VSM Upgrade for Battery Quality ComplianceCamel Group (BMW Battery Line), Xiangyang China, Energy & Construction
Information
Camel Group is a major Chinese supplier of automotive start-stop batteries, providing OEM solutions for brands like BMW. At its Xiangyang plant, the production line integrates electrode coating, cell formation, and final assembly under Class 100,000 cleanroom conditions.
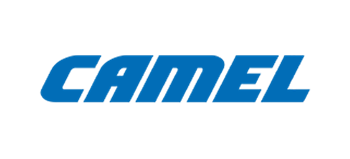
To address recent audit concerns and performance bottlenecks, Eddso deployed a hybrid approach combining VSM (Value Stream Mapping), TPM routines, and VDA 6.3 readiness improvement, with a special focus on cleanroom environmental control and visual process management.
Background
The site’s coating-to-assembly process suffered from unclear flow ownership, hidden waiting losses, and reactive quality control. Major challenges included:
- Disconnected Process Flow
Key steps (coating, drying, slitting, formation) lacked time sync and buffer logic. - Cleanroom Variability
Frequent airborne particle spikes led to unstable defect rates. - Low TPM Awareness
Maintenance relied on breakdown repairs; no PM matrix or responsibility layers. - Weak VDA Audit Performance
Documentation and traceability fell short of German OEM audit standards.
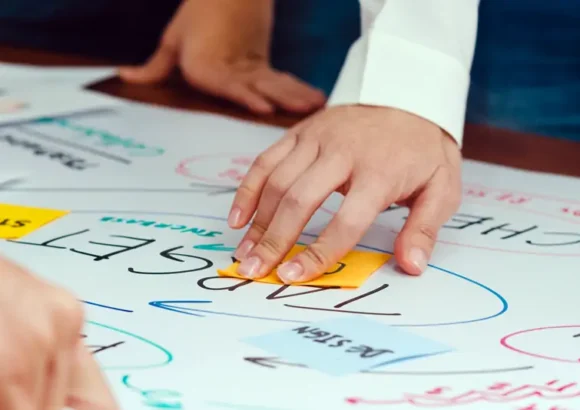
Value Stream Redesign & Audit Traceability
A full-stream VSM was conducted to map material and information flow from coating to final testing. The site took action on several critical issues:
- Streamlined Material Routes
Replaced point-to-point carts with central FIFO lanes and visual kanban triggers. - Built-in Quality Gates
Added checkpoint validations after drying and before assembly packaging. - Audit Backbone Construction
Created master process sheets, linked training records, and online defect logging in line with VDA 6.3 clauses 5–7.
TPM & Cleanroom Control
The coating area and assembly cleanrooms were upgraded to maintain Class 100,000 conditions with better equipment discipline:
- Visual TPM Boards
Operators received daily task charts, autonomous maintenance routines, and real-time alarms. - Airflow Control Maps
Dynamic zoning and humidity monitoring built into environmental dashboards. - Visitor Control Protocols
New PPE design kits and multilingual safety video were rolled out for cleanroom entry.
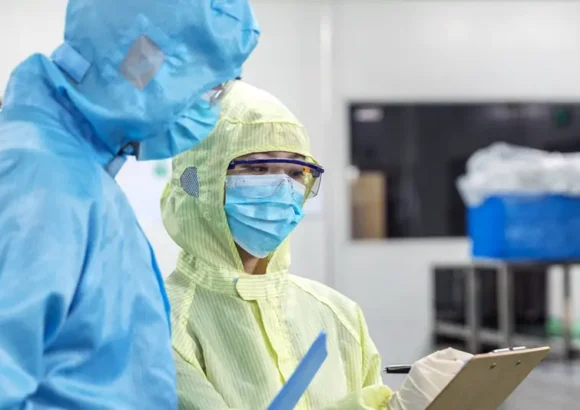
Project Benefits
- +32% Cleanroom Audit Score
VDA 6.3 clause scores increased from 61% to 93% in 6 months. - 14 Hours Lead Time Reduction
VSM helped eliminate redundant steps and queue time between coating and formation. - First-pass Yield ↑ by 36%
Coating NCs and misalignment defects significantly reduced. - Visual SOP & Ownership
100% operators now follow QR-coded SOPs with TPM cards and traceable job records.