Smart Supply-chain Resilience in Gear Shaft MachiningLinjiang Factory - Advance Gearbox, Hangzhou China, Energy & Construction
Information
Linjiang factory of Advance Gearbox, a key supplier for wind turbine gear shafts in China, struggled with fluctuating orders, inconsistent supplier lead-times, and overstocking at multiple process stages.

Eddso’s team deployed a layered approach to visualize material flow, classify supplier risk tiers, and build a predictive scheduling engine based on real-time consumption. The result: a stable, scalable and digitally visible supply network.
Background
The supply chain was fragmented across machining, heat treatment, and third-party inspection vendors, with minimal coordination and excess lead-time buffers.
- Fluctuating Customer Forecasts
Late changes from OEM clients caused schedule crashes and order reprioritization. - Overlapping Inventory Layers
Materials accumulated at each production stage due to lack of real-time planning. - Inconsistent Sub-supplier Commitments
Heat treatment vendors missed slots, causing backlog across the line. - No Tiered Risk Management
Supplier reliability was not quantified; all were treated equally in planning.
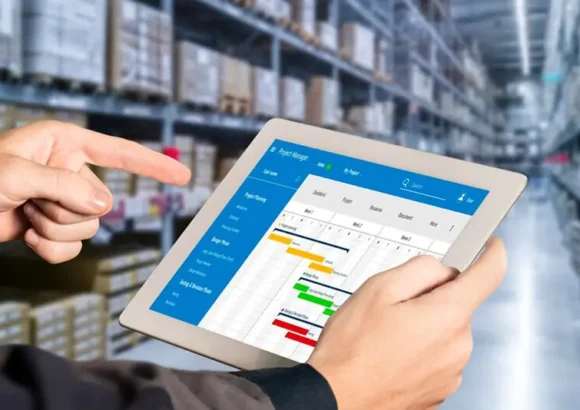
Inventory Heat Map
A layered digital solution enabled clear visualization of inventory risks and streamlined material flow across gear shaft production.
- Forecast Integration Engine
Integrated customer forecast changes with real-time production plans to reduce mismatch risks. - Real-Time Inventory Map
Mapped inventory accumulation and bottlenecks at each machining & heat-treatment stage. - Low-Code Scheduling Simulations
Built a low-code simulation platform for planners to adjust material flow based on SKU and order size, cutting changeover time by 30%.
Supplier Risk Management Platform
To strengthen delivery reliability and vendor tiering, a hybrid system integrating risk scoring and TPM routines was deployed.
- Supplier Tier Classification
Grouped vendors into Red-Yellow-Green tiers based on delivery scores and lead-time adherence. - TPM-Linked Reliability Checks
Added daily issue boards + real-time maintenance routines to address supplier-induced line stops. - Quick-Connect Layouts for Resilience
Equipment and handling zones were modularized to flexibly absorb disruptions from lower-tier vendors.

Project Benefits
Material lead time reduced by 22%, while supplier delivery stability improved by 35%.
- Stabilized Gear Shaft Delivery
Delivery stability improved from 81% to 94% over 3 months. - Lean Buffer Stock Strategy
WIP reduced by 15%, freeing 300㎡ of staging area. - Vendor Reliability Insights
Procurement now uses supplier risk scores to guide order volume allocation.