Restructuring Production & Logistics in Heavy Gearbox ManufacturingTiancheng Machinery, Jiangyin China, Machinery & Equipment
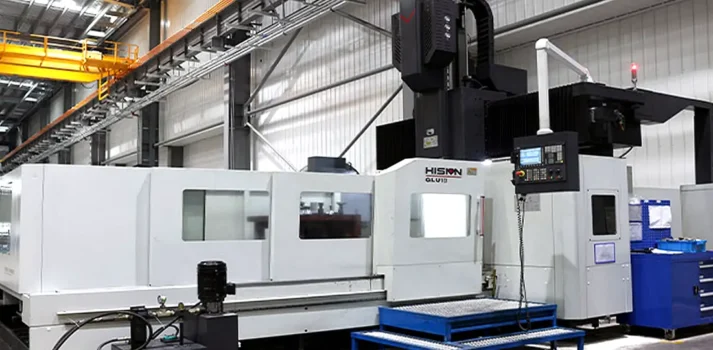
Tiancheng Machinery operates both legacy and new production facilities, manufacturing precision gearboxes for diverse heavy-industry applications. The company faced bottlenecks in scheduling and material flows across facilities due to production complexity and space constraints.
Eddso conducted a dual-factory optimization program focusing on smart scheduling, plant layout re-engineering, and visual management. A tailored approach was adopted to improve internal logistics, reduce congestion, and streamline assembly workflows.
Challenge
Legacy and new plants lacked integration in scheduling and layout, leading to delays and inefficient flows.
- Disconnected Production Islands
Departments were physically distant with mismatched production rhythms. - Inefficient Floor Usage
Legacy factory had low storage density and poor flow directionality. - No Unified Planning Tool
Production planning relied on spreadsheets, lacking real-time adjustment capability. - Limited Visual Guidance
Signage and workstation visibility were inadequate for coordination and oversight.
Solution
Eddso’s team implemented a comprehensive flow redesign and digital visualization strategy.
- Factory Flow Re-engineering
Redesigned plant layout using spaghetti flow analysis and lean zoning. - Dynamic Scheduling Board
Built real-time planning boards to align machining and assembly slots. - Smart Storage & Supermarket Zones
Introduced FIFO racks and route-based material handling systems. - Visual Management System
Designed cross-functional visual guides including signage, safety zones, and logistics coding.
- Factory Flow Re-engineering
Results
Tangible improvements in space utilization, scheduling stability, and visual transparency.
- +15% Throughput Capacity
Optimized floor use and synchronized shifts boosted output rates. - -30% Material Handling Time
Shortened movement routes and congestion relief. - Real-time Planning Accuracy
Live updates enabled quick adjustments to daily output plans. - Operator Empowerment
Visual guides improved cross-line coordination and reduced task ambiguity.