From Chaos to Flow: Lean Logistics & TPM at Dry BatteryMustang Battery Group, Ningbo China, Consumer Services & Lifestyle
Information
Mustang Battery is a global supplier of dry-cell batteries, including button cells, AA, and AAA types. Due to highly fragmented orders, complex packaging instructions, and frequent layout adjustments, the company faced mounting challenges in maintaining packaging efficiency and equipment reliability.
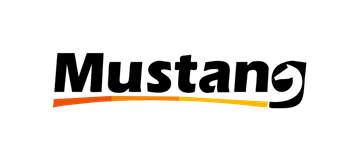
This project focused on streamlining internal logistics and optimizing the packaging area using TPM and lean digital principles.
Background
The packaging zone was overwhelmed by variability: mixed product specs, diverse blister pack configurations, and unpredictable changeovers.
- High Complexity of Packaging Materials
With over 120 packaging variants, operators wasted time locating and matching the correct inserts, stickers, or wrap formats. - Multi-SKU Mixed Packaging
Single orders often required multiple battery types in the same blister tray, leading to frequent manual sorting errors and rework. - Layout Inflexibility
The layout did not support quick reconfiguration; even minor adjustments required hours of teardown and reconnection. - Poor Equipment Reliability
Packaging line stoppages due to small but recurring issues (jammed sensors, feeding failures) significantly impacted OEE.
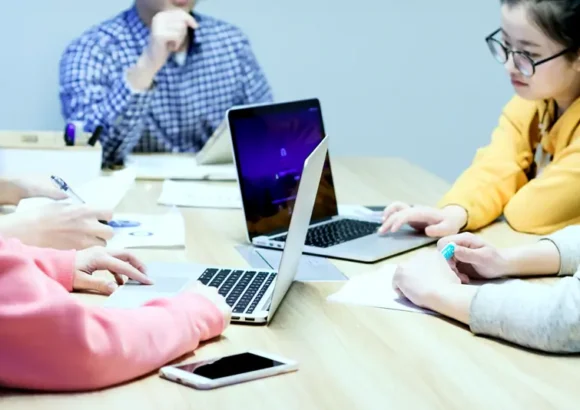
Scheduling & Logistics
To manage SKU complexity and support frequent packaging reconfigurations, Mustang redesigned internal logistics with modular material flow systems.
- Packaging Supermarket System
A centralized material storage was created to consolidate packaging variants and reduce search time errors. - Color-Coded Flow Routes
Dedicated carts and visual paths ensured mistake-proof movement between packaging lines. - Kanban Refill Loops
Lean-based replenishment system ensured JIT delivery and stabilized small-batch operations.
TPM & Lean Layout
A TPM-driven strategy and reconfigurable layout were applied to reduce stoppages and improve equipment response efficiency.
- Operator-Led Mini TPM
Daily level-1 checks improved lubrication, sensor alignment, and reduced micro-stoppages. - Quick-Connect Modular Layout
All key platforms and benches were made mobile and plug-and-play ready. - Issue Escalation Boards
Visual boards triggered maintenance response for unplanned minor stops.
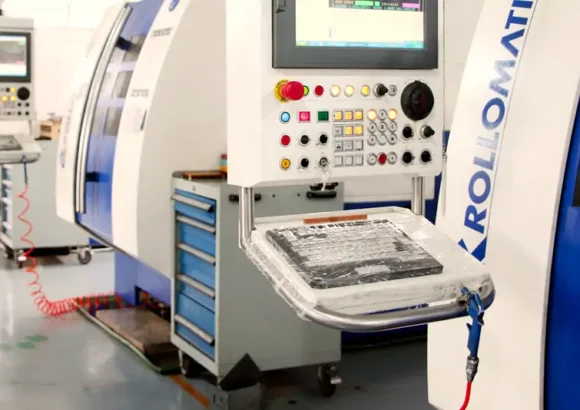
Project Benefits
Through lean logistics, TPM routines, and flexible layout design, the project delivered measurable improvements in performance and responsiveness.
- +25% Packaging Uptime
Line OEE improved from 62.4% → 79.5% in 3 months. - –45% Material Search Time
Search time per packaging variant reduced below 2 minutes. - Zero Unplanned Stops (Line 12)
TPM + escalation system achieved zero minor stops on high-priority lines.