Enhancing Cross-Factory Delivery for Denim OEM Supply ChainLucky Textiles Group – Wuxi & Yixing China, Apparel & Textiles
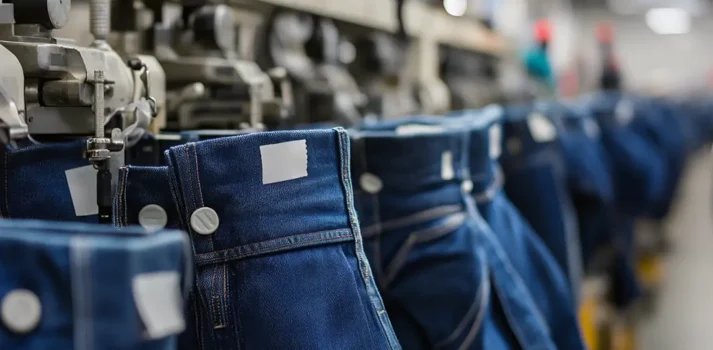
Lucky Textiles is a vertically integrated textile and apparel group serving international denim brands including Levi’s, Lee, Wrangler, Uniqlo, GAP and ZARA. With operations spanning fabric weaving, dyeing, and garment production across China and Cambodia, over 70% of its annual output is exported globally.
Eddso partnered with Lucky to enhance cross-factory synchronization between fabric and garment divisions. The goal was to stabilize OTD performance for multi-SKU export orders under brand pressure and to reduce production friction caused by misaligned schedules and style changeovers.
Challenge
Lucky’s full-chain production structure enabled control, but struggled with coordination across multiple business units and fast-changing client requirements.
- Fragmented Scheduling
Fabric mills and garment factories used separate planning systems with no common reference. - Frequent Style Changeovers
High-Mix-Low-Volume (HMLV) orders created constant SKU transitions on sewing lines. - OTD Deterioration
On-time delivery to US clients dropped below 88% for multi-factory orders. - Limited Client Visibility
Brand customers lacked access to real-time production milestones or slot status.
Solution
Eddso implemented a lean scheduling & OTD synchronization model across three countries and five business entities.
- Unified Planning Framework
Weekly schedule alignment across fabric, dyeing, and garment plants with lock-in periods and buffer logic. - SKU Mapping & Transition Planning
Built a “SKU family group” structure to minimize machine idle time and reduce style setup losses. - OTD Dashboard for Brands
Designed a shared-access platform showing cut-to-ship timelines and risk alerts for key client orders. - Client-Facing Supply Review
Established monthly delivery meetings with brand teams to review bottlenecks and forecast alignment.
Results
After implementation, Lucky restored delivery performance and improved brand-side confidence.
- +7% OTD Recovery
Orders delivered on-time rose from 87.6% → 94.8% within two quarters. - -22% Style Changeover Loss
Re-sequencing and setup balancing reduced changeover-induced downtime. - Faster Brand Communication Loop
Supply review and dashboards enabled real-time feedback and proactive escalation. - Cross-BU Process Discipline
Planning visibility enforced synchronized execution across weaving, dyeing and sewing.