Agile Quality Response in Precision Gear MachiningXiasha Precision Gears, Ningbo China, Machinery & Equipment
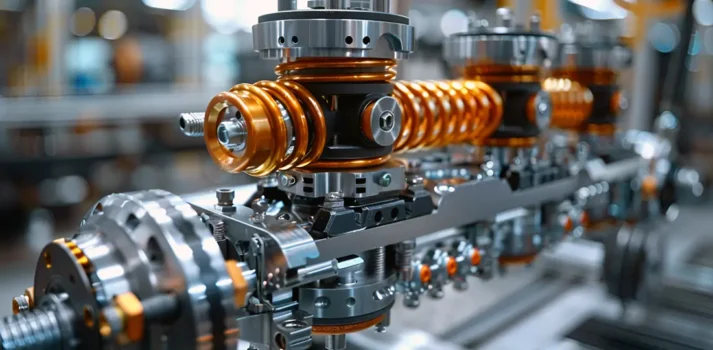
Xiasha Gear specializes in precision machining of micro-gear components used in robotics and medical automation. In early 2020, the company encountered inconsistent quality yields and a sharp rise in internal non-conformities (NCs).
Eddso implemented a fast-track quality response program targeting real-time defect identification, layered process audits, and operator training feedback loops. Within 6 months, first-pass yield improved by over 4%, and internal NCs decreased sharply.
Challenge
Xiasha Gear’s high-volume micro part production suffered from rising internal NCs, difficult-to-trace defects, and over-reliance on final inspection for quality control.
- Unstable Machining Process Windows
Tolerances were too tight for legacy equipment, leading to frequent rework. - Delayed Defect Feedback
Issues were detected too late during batch-end inspections. - Lack of Layered Audit Routines
Middle-layer supervision failed to catch systemic issues. - Operator Awareness Limitations
Quality standards and control points were not fully understood by frontline staff.
Solution
A short-term interim quality control roadmap was deployed, including root cause workshops, visual controls, and layered auditing.
- Quick-Response Quality Cells
Daily 10-minute defect huddles and feedback boards were introduced. - Process Window Validation (PWV)
Controlled trials to re-define critical machining tolerances for key parts. - Layered Process Audit (LPA)
Cross-functional auditing covering operators, line leaders, and engineers. - Visual Standard Work
Poka-Yoke visual guides and defect libraries placed on machines and checklists.
Results
A measurable uplift in quality consistency and agility in response was observed across lines.
- +4.1% First-Pass Yield
Yield rose from 92.1% to 96.2% over 6 months. - Reduced Internal NCs
Total internal NCs dropped by 37% in Q2. - Audit Coverage Tripled
Monthly audit coverage tripled from 2 to 6 lines, with full cross-functional involvement. - Shorter Feedback Cycles
Average detection-to-action response time reduced by 60%.