A Day in a Small Hydraulic Press Factory: Notes from a Logistics Assessment
- 10/21/2019
- Posted by: Charles.YANG
- Category: Field Practice
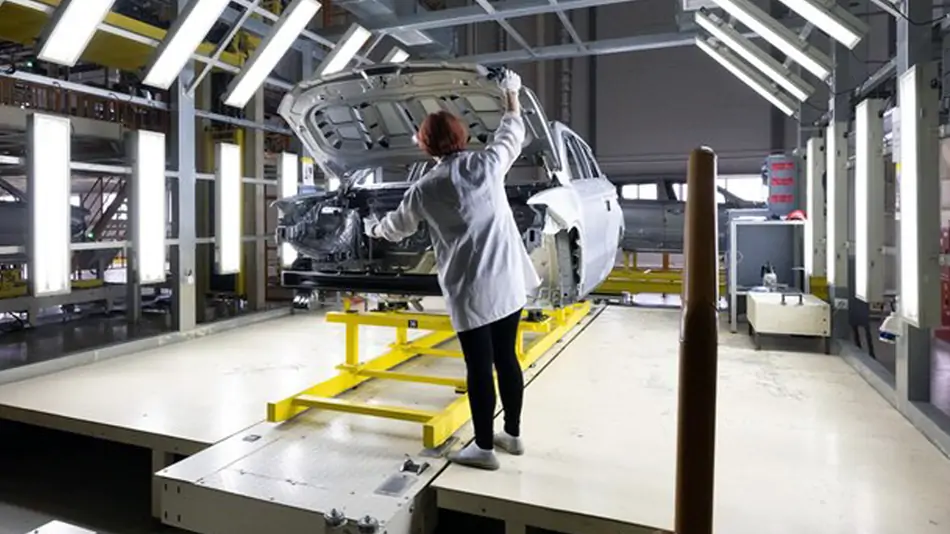
Some of the most insightful moments in consulting don’t happen in boardrooms—they happen while walking factory floors.
This is a brief field story from a one-day internal logistics assessment at a small hydraulic press manufacturer in Jiangsu, China. The factory, located in an industrial park an hour outside Wuxi, specializes in vertical and four-column presses for domestic and Southeast Asian markets.
What We Were Asked to Do
The client’s request was simple:
“We keep missing delivery deadlines! Can you help us optimize our internal logistics?”
They didn’t have a WMS (Warehouse Management System), and most movements relied on handwritten slips and forklift drivers’ memory.
We were there to observe and map material flow—from goods receiving to final assembly.
Observations on the Shopfloor
Here’s what we found after a few hours of on-site walkthrough:
- Incoming parts were mixed with rejected ones, with no clear quarantine zone.
- Large structural parts blocked aisleways, forcing forklifts to detour or reverse dangerously.
- No visual stock identifiers — everything looked the same, leading to frequent picking errors.
- Assembly stations lacked standardized Kanban, and one team lead literally walked 300+ steps/hour to fetch missing bolts.
Eddso’s Quick Response
We used our SO2: Internal Logistics Optimization toolkit to guide the client through an actionable improvement path:
- Created a spaghetti diagram to show excess travel & motion
- Re-zoned the warehouse into: Receiving / Quarantine / Main Inventory / Dispatch
- Introduced simple color-coded labels for component racks
- Marked one-way forklift paths using floor tape & 3-meter rule
- Standardized tool + fastener kits to reduce assembler motion by 42%
What You Can Learn from This Case
Even in small factories, internal logistics can account for 30–40% of total process time. You don’t need SAP to improve—you just need to observe, sketch, and act.
“The best layout is the one people don’t have to think about.”
Bonus Tip
One of the team leads said:
“I’ve worked here for 11 years. You’re the first outsider who followed a part from warehouse to machine.”
Sometimes, improvement starts by simply walking in the material’s shoes.