TPM and Ergonomics: How to Fix Problems Before They Break You
- 04/15/2022
- Posted by: Charles.YANG
- Category: Field Practice
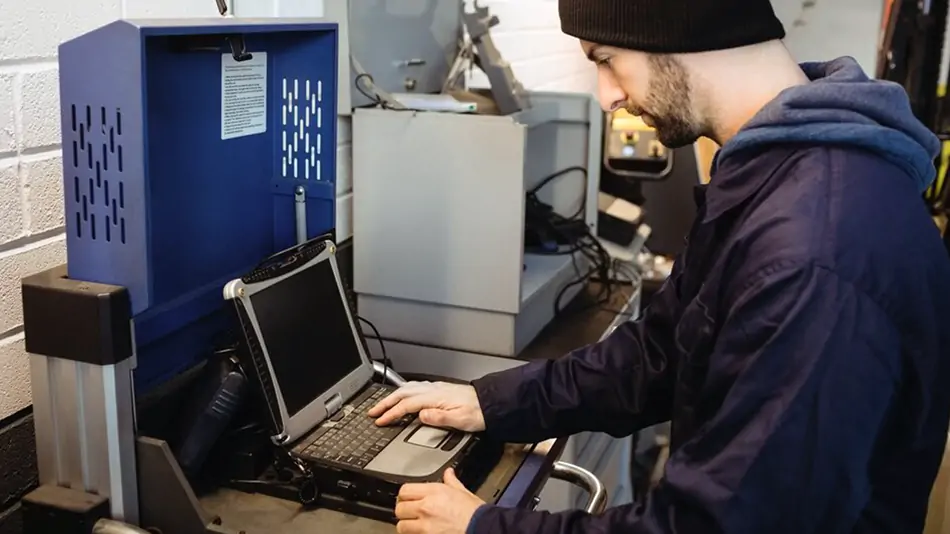
TPM and Ergonomics: How to Fix Problems Before They Break You
We were in a die-casting plant in East China.
The maintenance team proudly showed us their daily checklist.
The machines looked fine—until we saw the operator’s chair.
It had no back support. The man was leaning forward 30° for 8 hours a day, pulling parts from a poorly positioned chute.
“He’s our best guy,” the team lead said.
“He just doesn’t complain.”
He didn’t—but his spine will.
What We Usually See in Plants
Eddso’s TPM + Ergonomics assessments often find issues in three zones:
- Machines are over-maintained, but the operator’s tools are never reviewed
- Checklists cover grease points, but not motion stress or repetitive reach
- “Cleaning = TPM” mindset → true predictive diagnostics are missing
A Real Case: Packaging Line in Southern Jiangsu
Problem: Carton erector kept jamming every 3–4 hours
Reported Fix: Restart & clean sensors
Hidden Root Cause: Operator had to twist torso 60° to clear jams
- Result: Sensor cable wore out due to repeated tugging
- Side Effect: 2 back injuries in 6 months
We mapped the motion triangle, redesigned the reach zone, and shifted the machine 18 cm.
No more jams. No more injuries.
Our LS2: TPM & Ergonomics Diagnostic Covers:
- Machine status audit (run-time, downtime, MTBF)
- Operator movement mapping (MURI analysis)
- Posture & force risk scoring
- TPM role clarity & escalation path
- Kaizen roadmap with quick wins + long-term measures
What Clients Often Forget
- TPM ≠ cleaning alone
- A machine’s best “sensor” is still the operator
You can’t improve what people are afraid to report
“Before the machine breaks, the human already did.”
— Tony.ZHOU